Home / News / Industry News / Cast Aluminum Products And Their Uses
Cast Aluminum Products And Their Uses
Apr.14,2022
While you may not be aware of it, aluminum is the primary material used in many consumer goods and other products. Many car manufacturers are under increasing pressure to reduce their carbon footprint, which means they are looking to use lightweight aluminum components that can improve fuel efficiency. In addition to this, aluminum is also recyclable, making it a great choice for canning food. Listed below are some of the many uses for aluminum. Let's explore some of these uses in more detail.
Firstly, aluminum alloys are melted and then poured into molds to give a product its shape. Different processes are used to cast aluminum products, including permanent mold casting, sand casting, and sand casting. Another type of aluminum products is extruded, which uses a die to press hot billets of aluminum and other alloys through a die. This type of product can then be rolled, extruded, or forged into the desired shape.
Another type of aluminum product is the sandwich element. The sandwich element is manufactured by using foam and adhesive to fill a space between the layers of aluminum. It can be used in window blind profiles, bending strips, and welded walled tube.
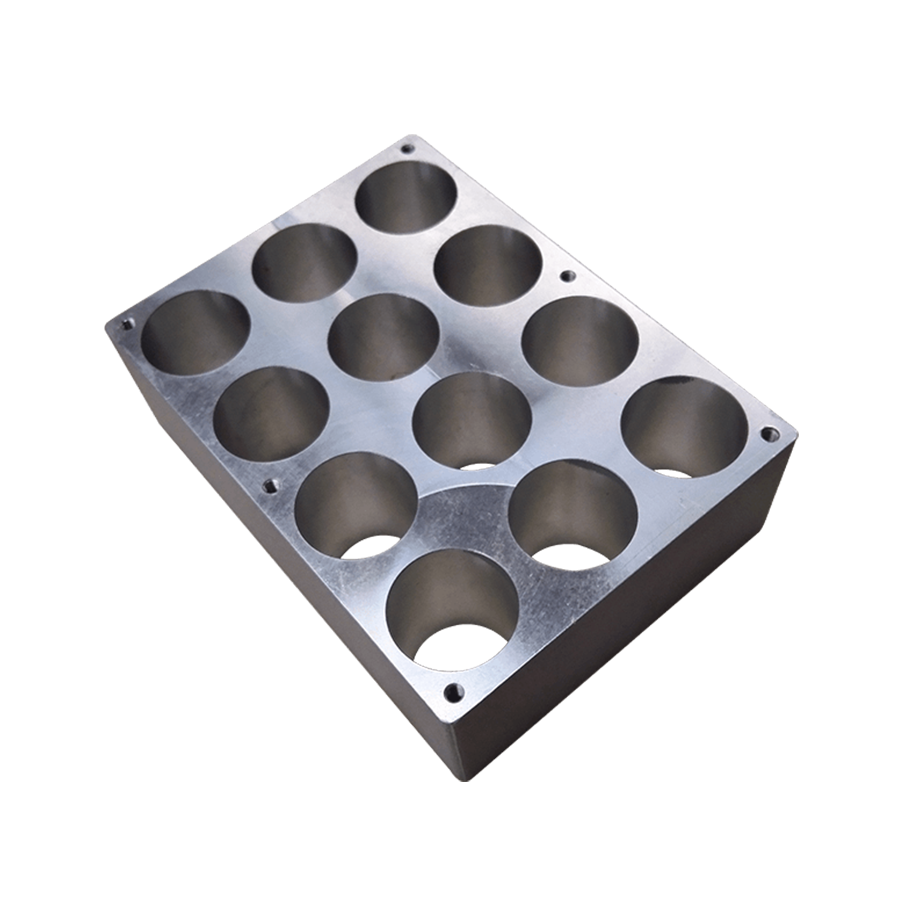
Despite its versatility, die casting is a less expensive option, but it is less adaptable than extrusion, which is why it is often used in low-volume production runs. Extrusions are more durable and can be used for smaller quantities, but they are often limited in their shapes. In addition, some extrusions may need additional post-forming machining in order to make them suitable for your final product. If you want your products to be stronger and lighter, though, the extrusion method is the way to go.
Reduction of alumina into metallic aluminum takes place in a steel vat called a reduction pot. The bottom of the reduction pot is lined with carbon, which serves as a conductor. The opposite electrodes are set up above the pot and are lowered into the electrolyte solution. The result is anhydrous aluminum crystal. After this process, the resulting product is transported to a cooling room. A reduction potline may produce 66,000 to 110,000 tons of aluminum annually.
Development of aluminum products has been essential to the aerospace industry for many years. From the Wright brothers' crankcases to modern commercial transport planes, aluminum has been used in various fields. And, the space industry has also been heavily dependent on aluminum products. Approximately 80 percent of commercial airplanes are made from aluminum, including their airframes and engines. And, the use of aluminum in aerospace has led to significant savings for producers of airplanes. There are several benefits to using aluminum in your manufacturing process.
Among the many uses for aluminum is diverse. The most widely used alloy is aluminum 3003, which is non-heat treatable and corrosion resistant. Other common uses of aluminum include cooking utensils and beverage cans. Aluminum 5052 has the highest strength and is excellently workable. It can also be drawn into complex shapes. And, it's highly resistant to corrosion in most environments, making it an excellent material for many applications.