Home / News / Industry News / Advantages Of A Custom Alloy Part
Advantages Of A Custom Alloy Part
Apr.07,2022
There are several reasons to order a custom alloy part. A manufacturer can't always order a material in advance from a supplier. Sometimes, they don't even have a stock of a part that meets their specific requirements. Custom alloy parts are an excellent alternative to the standard parts that most manufacturers stock. Not only are they more cost-effective and durable, they also provide a more appealing aesthetic to your product. Here are some of the advantages of a custom alloy part:
Hardfacing reduces wear
Among the many metalworking processes, hardfacing is an excellent way to decrease wear on custom alloy parts. Depending on the type of metal and the geometry of the part, hardfacing can be used to reduce wear, restore the dimensions of custom alloy parts, or repair worn components. Most hardfacing processes use nickel and cobalt based alloys, but advanced materials such as carbides and other niobium alloys can also be used for increased abrasion resistance. The process can be applied to both worn and newly manufactured pieces.
One type of hardfacing alloy is called martensitic hardfacing. It is applied in two or three layers. When used as a buffer layer, it is similar to the parent metal but can be used in unlimited layers. Its main function is to prevent check cracks from penetrating the parent metal. Hardfacing is used in combination with buffer layers to reduce wear on custom alloy parts. But before hardfacing, it is important to understand that buffer layers should never be made of mild steel. This is because mild steel is great for fabricating and joining, but they will collapse under the hardface layer.
Cobalt-chrome alloys are heat-resistant
The main benefits of cobalt-chrome alloys are their incredible strength, toughness and durability. They have superior hardness and are almost impossible to break, bend or deform. In addition, cobalt-chrome alloys are very appealing to the eye, with their white color and sheen resembling precious metals. CoCr alloys are widely used in the production of jewelry and are relatively inexpensive compared to other materials. However, some experts do not recommend them for use in jewelry.
Cobalt-chrome alloys have excellent corrosion resistance and are often used in applications that require high-strength and heat resistance. They are biocompatible, wear-resistant and chemically inert, and exhibit excellent mechanical properties. Among the applications for cobalt alloys include cutting tools, high-performance engines and sturdy gun barrels. Additionally, cobalt-chrome alloys are extremely durable and are used in many types of cutting instruments.
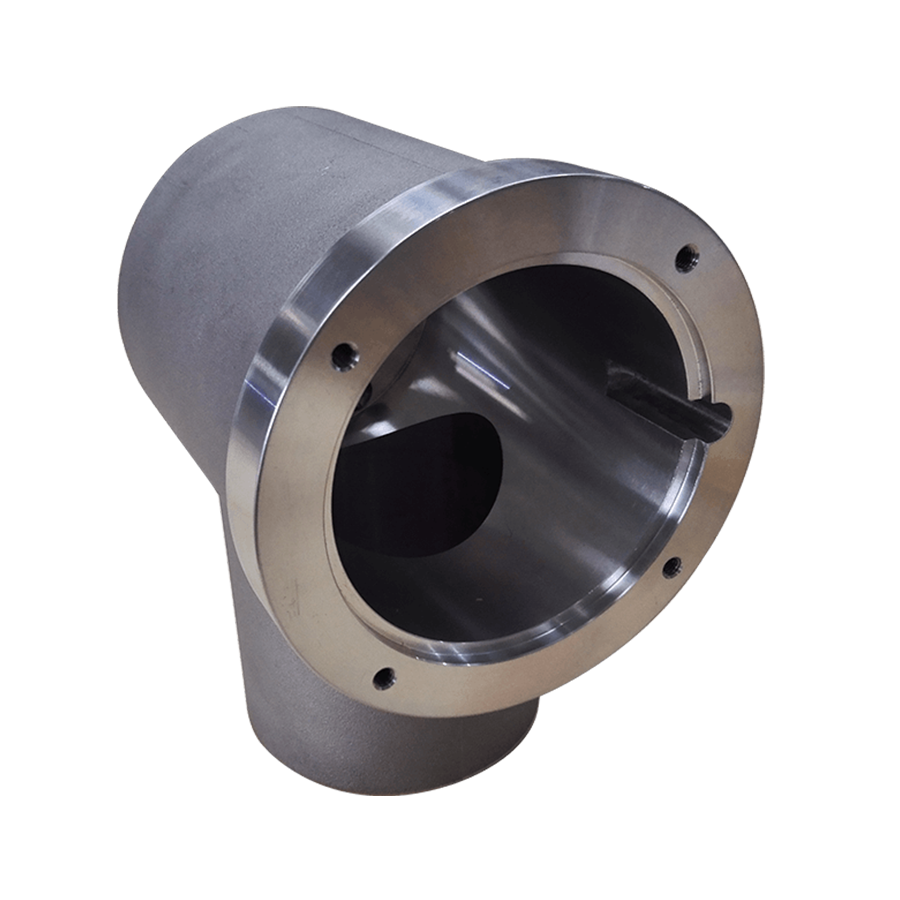
Main body of meat grinder
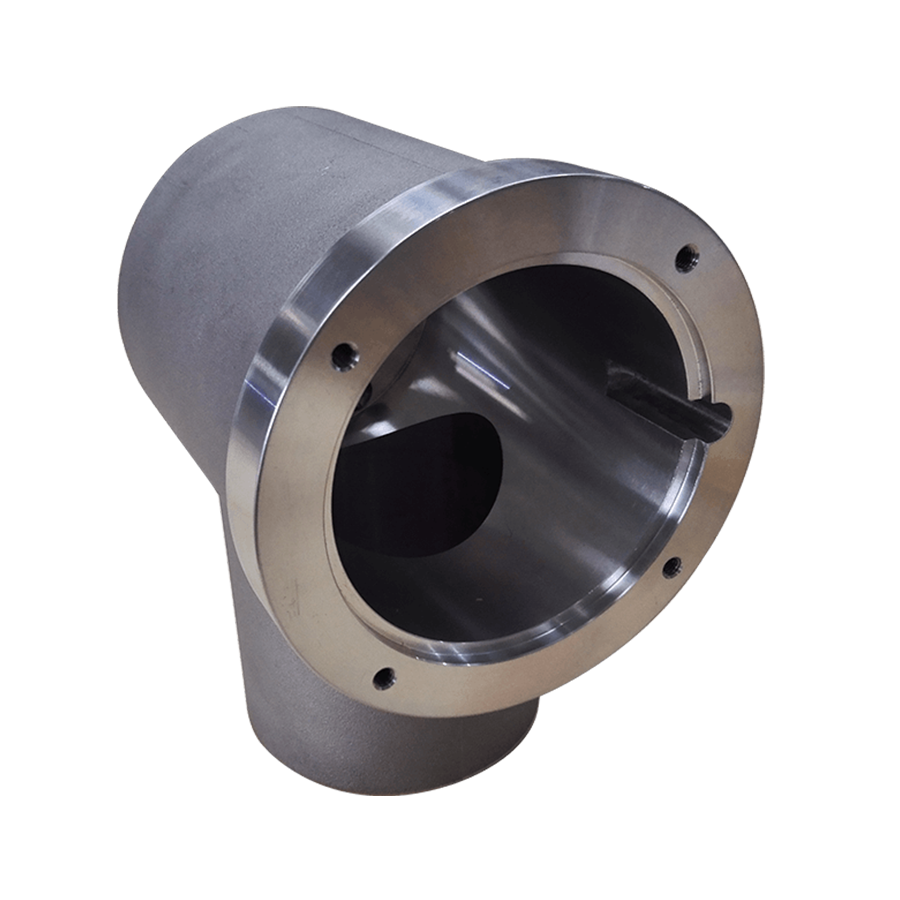
Main body of meat grinder
CNC stainless steel
A CNC stainless steel alloy part requires a high level of precision to ensure the part's quality. This material is one of the hardest metals to machine, but following best practices can improve machinability. Proper cutting geometry, tooling, and feed rates are crucial to a successful CNC machined part. The inclusion of sulfur, copper, and lead in the alloy can influence machinability, as they reduce ductility and allow chips to break away easier.
Stainless steel is available in many grades, including alloy 304. Alloy 304 has 18% chromium and 8% nickel, with a maximum carbon content of 0.07%. CNC machining can yield superior formability, and 304 is easy to weld. Resistance welding processes are available for machining parts made of this material. Alloy 17-4 PH stainless steel is a precipitation-hardening, austenitic alloy that offers excellent corrosion resistance and wear resistance.
Forged aluminum components provide an attractive appearance
A number of advantages of forged aluminum components make them an excellent choice for structural applications. Among them are the light weight, high strength, and attractive appearance of the parts. Another benefit is their relatively low cost. Moreover, they are used for a wide range of applications that demand high integrity and durability. Deeco Metals specializes in high-volume production runs and customization of unique shaped aluminum machined forgings. These companies can produce almost any forged aluminum component required by customers.
Another benefit of forged aluminum is that it does not restrict the flexibility of a component's design. Unlike casting, forging allows designers to create complex shapes without limiting the ability of a component's design to fit the mold. Moreover, forged aluminum alloys demonstrate mechanical properties that are comparable to those of steel. Additionally, the strength-to-weight ratio of aluminum is greater than steel. Lastly, forged aluminum components have a high degree of design flexibility, as they do not require extensive polishing.