Home / News / Industry News / There are several factors that affect the cost of die casting an aluminum alloy.
There are several factors that affect the cost of die casting an aluminum alloy.
Oct.08,2022
Die Casting Aluminum Alloy Parts
There are several factors that affect the cost of die casting an aluminum alloy. First, it's important to have a mold that is efficient and easy to use. This will ensure that the melted aluminum can be injected properly and that the built-up part can be easily removed. The next factor to consider is where to inject the melted aluminum. The more injection points you have, the less likely the aluminum will solidify in the crevices of the die.
The design wall thickness of an aluminum alloy die casting part is also important. Thin walled castings can have weak structures and can easily deform. Therefore, it's essential to use stiffeners in order to prevent deformation and improve strength. Reinforcement ribs are also useful in improving stress distribution. They also help in the flow of the molten metal and improve filling performance.
Besides being lightweight, die-cast aluminum parts are aesthetically pleasing and corrosion-resistant. However, a proper finishing process can help improve the functional properties of aluminum alloy die-cast parts. For example, applying a chrome finish to aluminum die-cast parts will make them more resistant to corrosion.
Another option for improving the performance of aluminum alloy die-cast products is applying a conversion coating. This process can be used as a pre-finish for other surface finishes or as the final finish. These surface finishing techniques are designed to improve corrosion resistance, surface performance, and insulating properties. Each surface finish method has its own advantages and disadvantages.
Aluminum alloy die casting is an increasingly popular process for manufacturing industrial and building parts. This method offers high production efficiency and excellent dimensional accuracy. It also offers superior strength at high temperatures and good flexibility. Additionally, die-cast aluminum is an excellent choice for automotive parts. So, it's important to choose the right aluminum alloy for your project carefully.
The process of aluminum die casting begins with a mold. Using high pressure, aluminum metal is poured into the mold and solidifies. Die-cast aluminum parts require little machining and are highly accurate. They are also cheap to manufacture, which makes them ideal for high-volume production. Aside from being easy to produce, die-cast aluminum parts can be molded into complex shapes. They are durable and have good surface finish.
In addition to die-casting parts, aluminum alloy die casting can be used for an extensive range of products. Some of these products include engine fittings and valve bearings. Other applications include building parts and guardrail accessories. These products can also be found in the automotive industry. If you're looking for a new car or a new truck, aluminum alloy die casting can help.
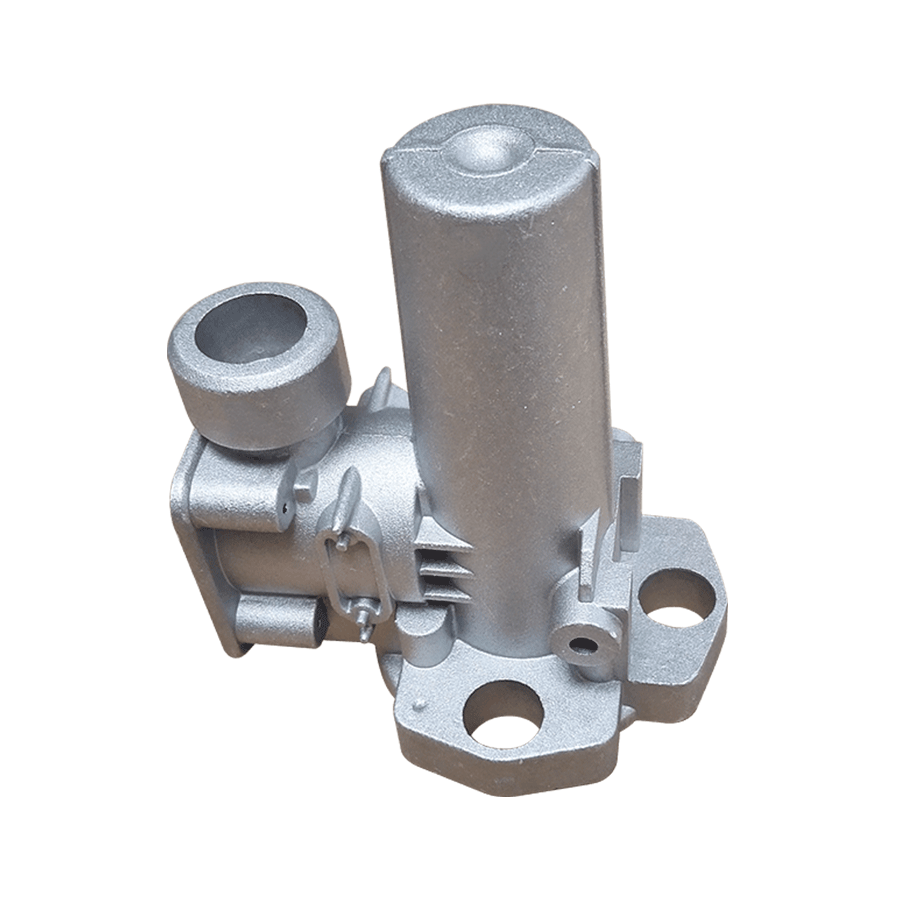
Electric digging valve
Casting process:High-pressure casting
Approximate weight:0.65kg
Approximate size:200x100x80
Application:Auto parts