Home / News / Industry News / The Advantages of Cast Valve Parts: Why They're the Smart Choice
The Advantages of Cast Valve Parts: Why They're the Smart Choice
Jun.14,2023
In various industries such as oil and gas, petrochemical, and power generation, valves play a critical role in controlling the flow of fluids and gases. Valves are comprised of various components, and one key consideration when it comes to their production is the choice of valve parts. While there are different manufacturing methods available, cast valve parts offer numerous advantages that make them the smart choice for many applications.
Design Flexibility: Cast valve parts offer unparalleled design flexibility. The casting process allows for the creation of complex geometries and intricate internal structures that may not be easily achievable with other manufacturing methods. This versatility enables engineers to design valves with optimized flow characteristics, enhanced sealing capabilities, and improved performance.
Material Variety: Cast valve parts can be manufactured from a wide range of materials, including various metals and alloys. This flexibility in material selection allows engineers to choose the most suitable material for the specific application requirements. From stainless steel to bronze, cast valve parts can be tailored to provide the desired mechanical properties, corrosion resistance, and temperature or pressure resistance, ensuring the valves perform optimally in challenging environments.
Cost-Effectiveness: Casting is a cost-effective manufacturing method for producing valve parts, especially in high-volume production. The process allows for the production of complex parts in a single piece, eliminating the need for multiple machining operations and assembly. This reduces production time, labor costs, and material waste. Additionally, casting enables the use of less expensive raw materials, further contributing to cost savings.
Strength and Durability: Cast valve parts exhibit excellent strength and durability. The casting process allows for the formation of a dense and uniform microstructure, resulting in parts with high mechanical integrity. This ensures that cast valve parts can withstand high-pressure and high-temperature conditions, as well as endure prolonged operation without failure. The inherent strength of cast valve parts also contributes to their resistance to wear, erosion, and corrosion.
Consistency and Quality: Cast valve parts can be manufactured with high precision and repeatability. Modern casting techniques, such as investment casting and lost foam casting, ensure tight tolerances and excellent surface finishes. This consistency in manufacturing quality leads to valves with reliable performance, minimal leakage, and extended service life.
Rapid Prototyping and Customization: Cast valve parts offer the advantage of rapid prototyping and customization. With casting, it is possible to produce functional prototypes quickly, allowing for design validation and performance testing before committing to full-scale production. Moreover, cast valve parts can be easily customized to meet specific project requirements, whether it is adjusting dimensions, modifying internal features, or incorporating company logos or branding.
In conclusion, cast valve parts offer numerous advantages that make them the smart choice for valve manufacturing. Their design flexibility, material variety, cost-effectiveness, strength and durability, consistency and quality, as well as rapid prototyping and customization capabilities, position them as a preferred option in various industries. When it comes to selecting valve parts, considering the benefits of cast components can lead to improved valve performance, reduced costs, and enhanced operational efficiency.
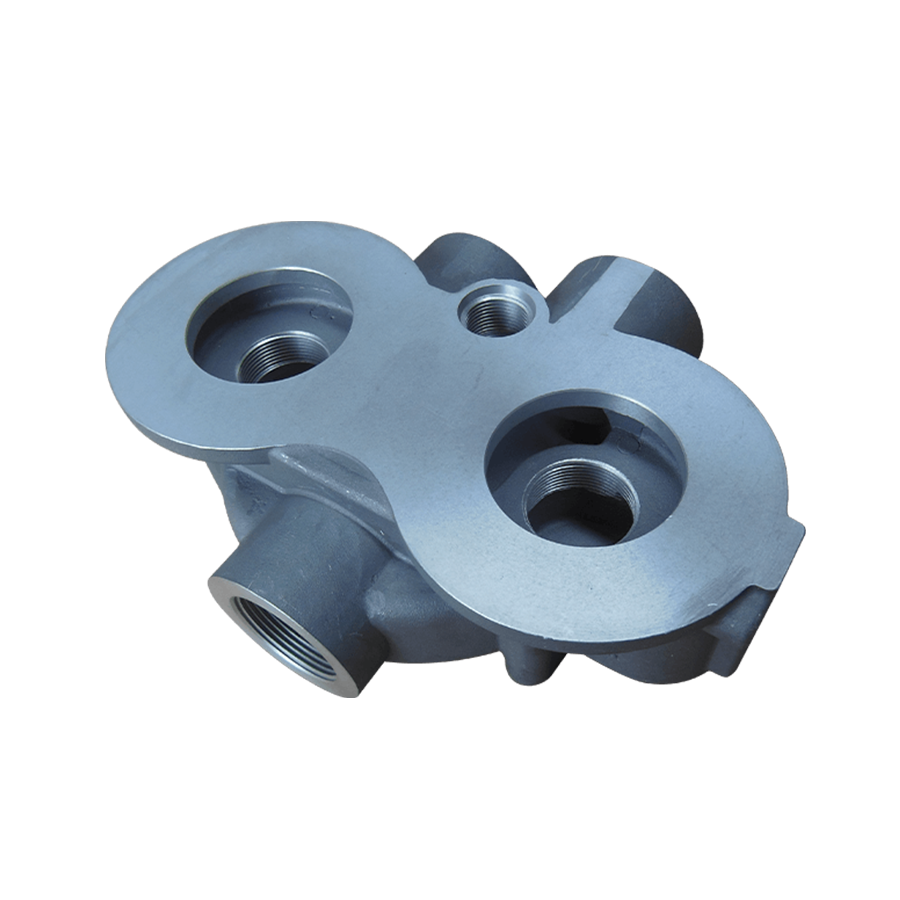
Casting process:Low-pressure casting
Approximate weight:3.8kg
Approximate size:220x250x100
Application:Water treatment equipment