Home / News / Industry News / Fluidity And Shrinkage Of Aluminum Alloy Casting
Fluidity And Shrinkage Of Aluminum Alloy Casting
May.31,2022
Fluidity Fluidity refers to the ability of the alloy liquid to fill the mold. The fluidity determines whether the alloy can cast complex castings. The fluidity of eutectic alloys in aluminum alloys is better. There are many factors that affect the fluidity, mainly the composition, temperature and solid phase particles of metal oxides, metal compounds and other pollutants in the alloy liquid, but the external fundamental factors are the pouring temperature and pouring pressure (commonly known as pouring head) the level of. Shrinkage Shrinkage is one of the main characteristics of cast aluminum alloys.
Generally speaking, the alloy is divided into three stages from liquid casting to solidification, until cooling to room temperature, namely liquid shrinkage, solidification shrinkage and solid state shrinkage. The shrinkage of the alloy has a decisive influence on the quality of the casting, which affects the size of the shrinkage cavity, the generation of stress, the formation of cracks and the change of the size of the casting. Usually casting shrinkage is divided into volume shrinkage and linear shrinkage. In actual production, linear shrinkage is generally used to measure the shrinkage of the alloy. The shrinkage of aluminum alloys, usually expressed as a percentage, is called shrinkage.
Body shrinkage Body shrinkage includes fluid shrinkage and coagulation shrinkage. From pouring to solidification of casting alloy liquid, macroscopic or microscopic shrinkage will appear in the solidified place. This macroscopic shrinkage cavity caused by shrinkage is visible to the naked eye, and is divided into concentrated shrinkage cavity and dispersed shrinkage cavity. The hole diameter of the concentrated shrinkage cavity is large and concentrated, and is distributed at the top of the casting or at the hot joint with thick section.
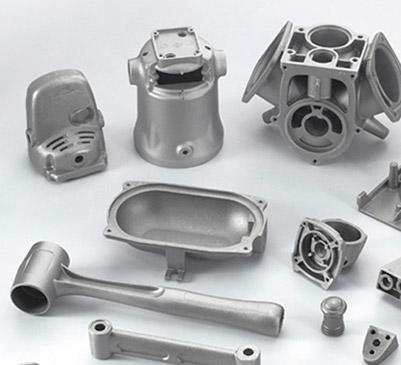
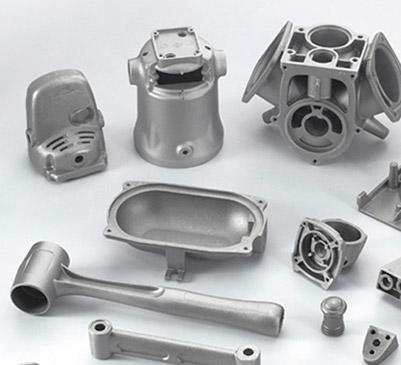
The morphology of dispersive shrinkage cavities is scattered and small, and most of them are distributed in the casting axis and hot joints. The microscopic shrinkage holes are difficult to see with the naked eye, and most of the microscopic shrinkage holes are distributed under the grain boundaries or between the dendrites of the dendrites. Shrinkage cavities and porosity are one of the main defects of castings, which are caused by the fact that the shrinkage in the liquid state is greater than that in the solid state.
It is found in production that the smaller the solidification range of the cast aluminum alloy, the easier it is to form concentrated shrinkage cavities, and the wider the solidification range, the easier it is to form dispersed shrinkage cavities. The bulk shrinkage from liquid to solidification should be supplemented by the alloy liquid, and shrinkage cavities and porosity are concentrated in the outer riser of the casting. For aluminum alloy castings that are prone to disperse porosity, the number of risers should be more than that of concentrated shrinkage holes, and cold iron should be set in the place where porosity is likely to occur to increase the local cooling rate to make it solidify at the same time or quickly.
Line shrinkage The size of line shrinkage will directly affect the quality of the casting. The greater the linear shrinkage, the greater the tendency of the aluminum casting to produce cracks and stress; the greater the size and shape change of the casting after cooling. Different casting aluminum alloys have different casting shrinkage rates. Even if the same alloy has different castings, the shrinkage rates are also different. On the same casting, the length, width and height shrinkage rates are also different. It should be determined on a case-by-case basis.