Home / News / Industry News / Cast aluminum alloy motor parts provide a range of benefits for vehicle owners.
Cast aluminum alloy motor parts provide a range of benefits for vehicle owners.
Nov.01,2022
Cast Aluminum Alloy Motor Parts
Cast aluminum alloy motor parts provide a range of benefits for vehicle owners. These parts feature low weight, high strength, and excellent machinability. In addition to these benefits, casting aluminum offers several other advantages over conventional construction methods. The company LeClaire Manufacturing specializes in these parts for a variety of automotive applications. Consumer car engine casting is one of the most common uses, but aluminum engine castings are also found in many other automotive applications.
Cast aluminum alloy is commonly used in car parts, including engine components, transmission parts, and suspension elements. These lightweight parts help reduce vehicle weight and improve safety. They can also be produced in high volumes, with hundreds to thousands of parts produced daily. They can also be used in medical devices, as they are both light and heat-resistant. Common medical equipment made of aluminum includes medical tools, hospital bed gearboxes, and pumps.
Another benefit of aluminum is its corrosion resistance. While steel and iron components are easily corroded by moisture and other substances in the air, cast aluminum parts are rarely affected by corrosion due to a thick oxide layer. Furthermore, aluminum castings are suitable for various surface treatments, including painting and anodizing. This means that cast aluminum auto parts offer more corrosion resistance, which is an important benefit for motorists.
Cast aluminum alloys have a number of advantages, including good castability and low melting point. The alloys are also relatively fluid, resulting in short casting cycles and good as-cast surface finish. These properties help make them a competitive alternative to welded assemblies. But there is one drawback to aluminum alloys: they are susceptible to corrosion, so it is important to choose the right one for your needs.
Cast aluminum alloys undergo a number of processes before being put to use. The first is a process known as cold curing, which is usually 8 hours long. The second process is called precipitation hardening. This process removes oxides, and changes the microstructure of the metal.
Another method is to clean aluminum parts using vinegar. Combine a quart of vinegar with a cup of water, then allow the mixture to boil for 15 minutes. Then, soak an aluminum part in the solution for some minutes. Large aluminum surfaces can also be cleaned with a cloth soaked in the mixture. Then, dry the part with a clean rag.
Cast aluminum alloys are more durable and versatile than regular aluminum. They are more resistant to heat and corrosion and are inexpensive to repair. In addition, they are environmentally-friendly. Nearly all aluminum is recycled in the U.S. This material is also widely used for similar applications as aluminum.
There are several different types of heat treatments that can be used for casting aluminum alloys. The most common is high-pressure die-casting, which produces parts in the as-cast condition. However, high-pressure die-casting can produce parts with artifacts and render heat treatment unnecessary. Other types of heat treatment can result in increased hardness and dimensional stability.
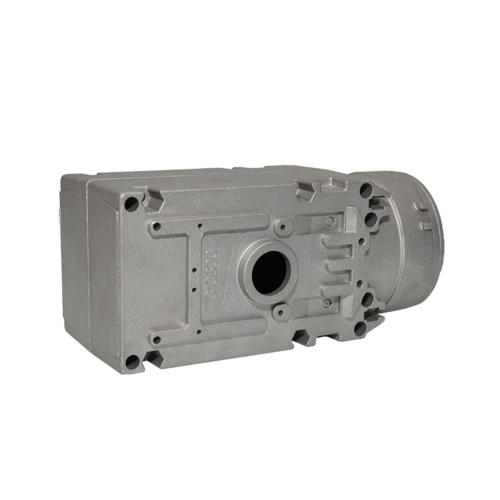
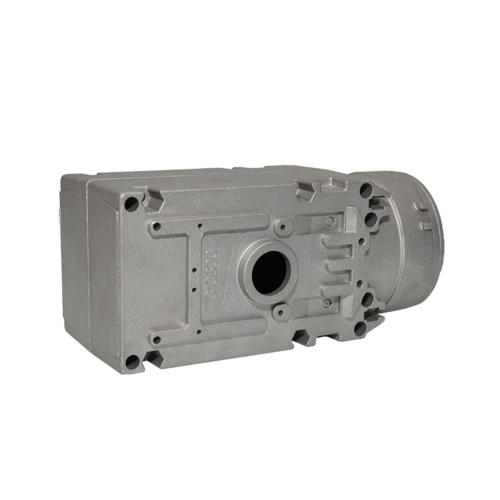