Home / News / Industry News / Aluminum alloy die-casting parts are also cost-effective.
Aluminum alloy die-casting parts are also cost-effective.
Dec.22,2022
Whether it's for electronics housings, portable consumer goods, fuel-efficient vehicles, or construction elements, aluminum die casting parts are important. The aluminum alloy is lightweight, corrosion-resistant, and offers good strength to weight ratio. These properties are particularly important for mass-manufactured consumer appliances and fuel-efficient vehicles.
Aluminum alloys have a wide range of properties, including hardness, strength, ductility, fluidity, and melting point. These properties determine the final product's mechanical and functional performance. However, aluminum die casting is susceptible to surface defects and imperfections. The resulting defects can influence the mechanical properties, appearance, and cost of the die cast.
In order to improve the overall performance of the die cast, several surface finishing techniques can be used. The surface of the die cast can also be enhanced with corrosion resistance and heat resistance. These features can help protect the environment and improve functional performance.
In order to prevent cracks and other defects on the surface of the die cast, the thickness of the die casting wall must be uniform. It should also be rounded in the corners. This will help prevent defects caused by the forging ground stress.
The thickness of the die casting wall also affects the draft angle. Normally, the inner cavity exit angle is about half of the outer surface exit angle. A greater draft angle results from a higher melting point. In addition to this, the thickness of the casting wall affects the calculation of filling time.
In the early stages of mold design, the parting line must be considered. This line divides the mold into two separate parts. If the molten metal fills a gap before the die cast is ready to be separated, the injection points must be chosen carefully. If a cavity is designed, multiple injection points can be advantageous.
Adding ribs to the die casting mold can also help improve its filling performance. These ribs can improve stress distribution and prevent root fracture. They can also be used to enhance the properties of thick-walled pipes.
Aside from this, stiffeners can also be used to prevent deformation. These stiffeners are often used to minimize the size of the die cast and ensure its long-term functionality. The use of stiffeners also helps to improve the strength of the die-casting process.
Aluminum alloy die casting products can be improved by adding a protective coating. For example, a clear anodized coating can be used to improve the appearance of the die cast. However, the coating must be uniform, bright in color, and resistant to prolonged heating. Electroplating can also be used to improve the surface of the die cast.
Aluminum alloys have different properties, so the choice of alloy must be made carefully. These properties determine the final product's strength, hardness, and mechanical and functional performance. The alloy properties must also be uniform, and the density must be appropriate for the final product.
Aluminum alloy die-casting parts are also cost-effective. This is because they are produced with low processing costs and high dimensional accuracy. Their high efficiency is one of the reasons they are used in the aerospace, building, and automotive industries.
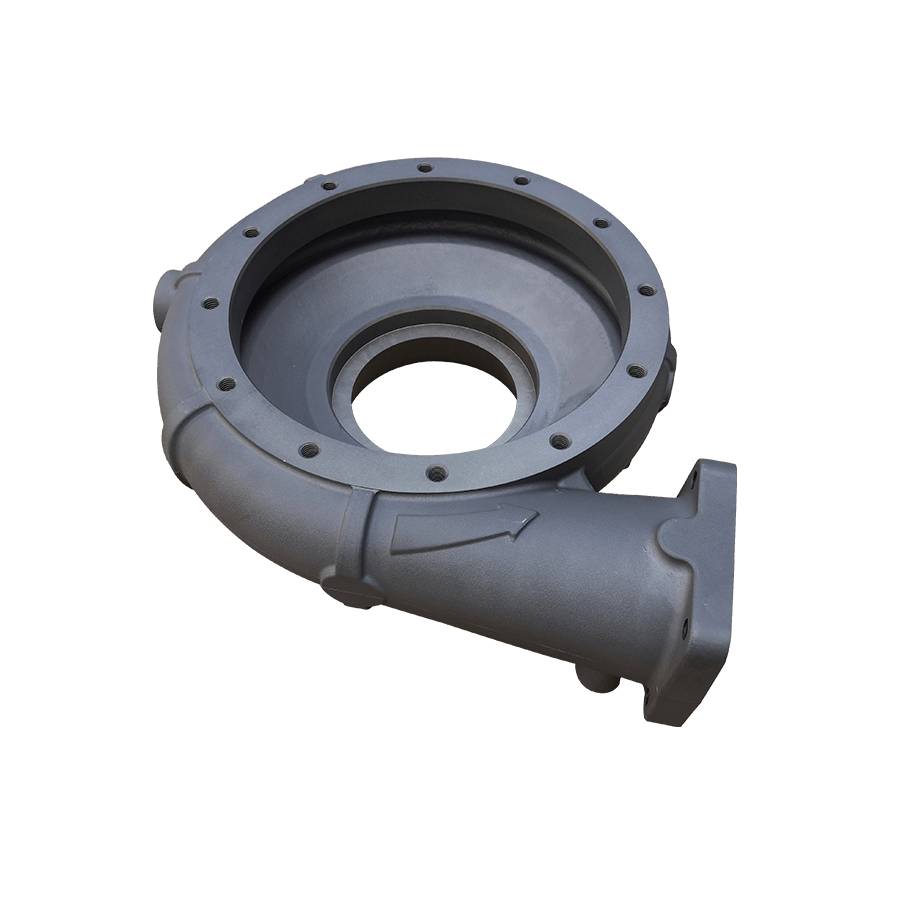
High pressure volute
Casting process:Low-pressure casting
Approximate weight:12kg
Approximate size:φ520x150
Application:Water treatment equipment