Home / News / Industry News / Aluminum Alloy Die Casting Parts are made from aluminum alloy
Aluminum Alloy Die Casting Parts are made from aluminum alloy
Sep.08,2022
Aluminum Alloy Die Casting Parts are made from aluminum alloy. The process can be performed in a variety of capacities. A single die can produce hundreds or thousands of parts. The initial tooling time can range from four to twelve weeks. Once the die is ready for production, samples can be ordered. A final approval process usually occurs in two weeks.
During the process, die casters perform secondary operations, such as taping holes and polishing. These operations allow for better filling of the parts' surfaces. Another advantage of die casting is that it can produce parts with tight tolerances. It is also possible to cast parts with complex shapes.
Aluminum Alloy Die Casting Parts are used in many industrial applications, including aerospace. They offer lightweight construction while maintaining tensile strength. Choosing the appropriate surface finish for aluminum die cast parts is a key decision. While aluminum die casting produces an excellent surface finish by casting standards, there can be some imperfections. Sandblasting, orbital sanding, and other finishing methods can be used to improve these imperfections.
Another industry that benefits from aluminum die casting is the building and construction industry. The process is used in prefabricated buildings, windows, curtain walling, and shop partitions. In the aerospace industry, aluminum die casting parts are integral to air-frame components. Their lightweight properties help make them durable and cost-effective.
The main defects that occur in die-cast aluminum alloy parts are irregular flows and low temperatures. These types of defects can affect the aesthetic quality and strength of the parts. When high temperatures are not reached during die-casting, air pockets can develop in the cast material. If they are not removed, the aluminum alloy may lose its structural integrity.
Aluminum Alloy Die Casting Parts are made of several different types of aluminum alloys. Alloy 380 is the workhorse of aluminum alloys and offers the best combination of casting and product properties. It is used in a variety of industries and is a popular choice for aircraft components. Another alternative to 380 is Alloy 383.
The advantages of aluminum die casting include its high strength-to-weight ratio and low density. Aluminum is also a durable material and has excellent electrical conductivity. It is also widely used in the automotive industry. In addition, it is lightweight and corrosion-resistant. In addition, it is recyclable.
Aluminum Alloy Die Casting Parts are increasingly used for manufacturing automobile components. The production of these parts is increasing. Automobile manufacturers are increasingly seeking ways to make their products lighter, more fuel-efficient, and more reliable. In addition, they are also seeking new ways to reduce their carbon footprint.
Aluminum Alloy Die Casting Parts are made of different types of aluminum alloys. Among the most common alloys for aluminum die casting are A380, b390, and A413
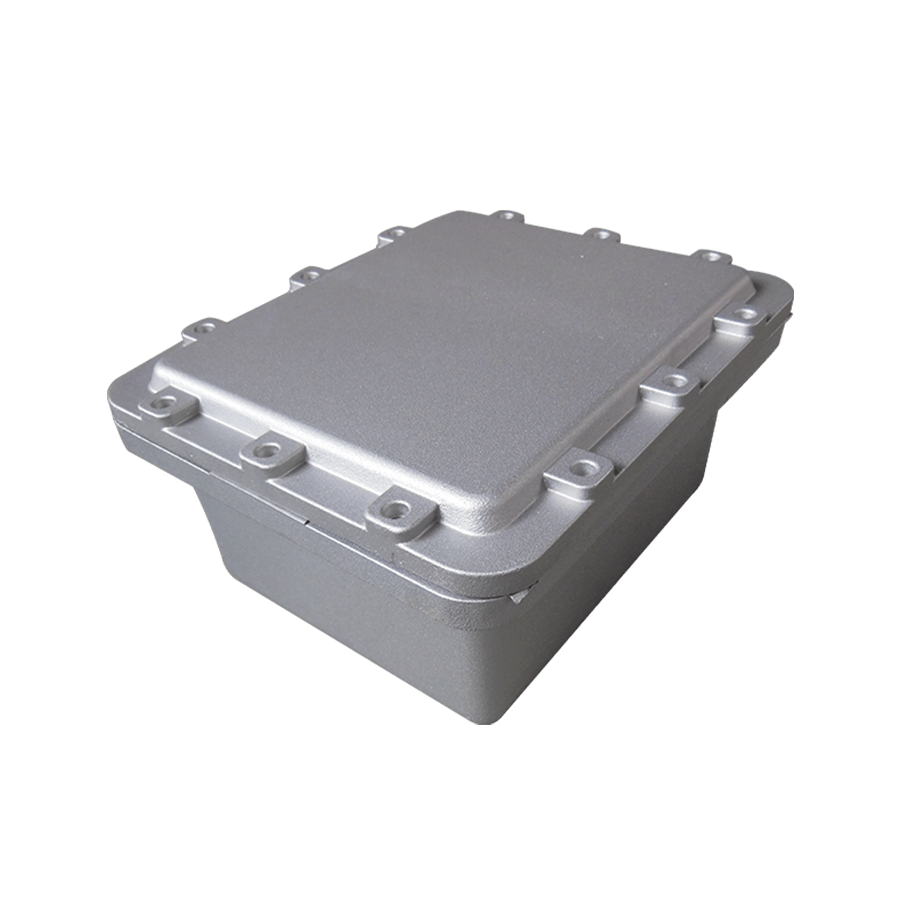
Explosion-proof box
Casting process:Low-pressure casting
Approximate weight:8kg
Approximate size:300x220x190
Application:Explosion-proof electric box
Product Description
Casting process |
Approximate weight |
Approximate size |
Application |
Low-pressure casting |
8 |
300x220x190 |
Explosion-proof electric box |