Home / News / Industry News / Advantages of Aluminum Alloy Sand Casting Parts
Advantages of Aluminum Alloy Sand Casting Parts
Aug.10,2022
The process of making aluminum alloy sand casting parts involves the use of high pressure die casting. The process is done by a foundry in China. After the parts have been cast, they are fabricated using CNC machines, milling machines, drills, and lathes. The quality of the finished product depends on its ductility and strength. To improve its quality, engineers must overcome its disadvantages and promote its benefits.
The process begins with a pattern made from a metal or thermosetting phenolic resin. The mold is then coated with a lubricant and placed in a thermoset sand chamber. After a few minutes, the mold is turned upside down to solidify. The pattern is then removed from the mold. The two halves form the mold. Next, liquid aluminum is poured into the mold cavity, where it solidifies to form the casting.
The cost of aluminum sand casting tooling is $500 to $7,500, depending on complexity. In contrast, aluminum die casting tooling costs $5,000 to $75,000 and can yield up to one million parts. Another benefit of aluminum sand casting is that it is much cheaper and faster to build. The process also reduces production costs as the molds can be discarded. The process is capable of producing thousands of parts per day.
Another major benefit of aluminum sand casting is the ability to produce many types of aluminum parts. Compared to other metals, aluminum is more useful for gear housings as it withstands high temperatures and is also lightweight. Another benefit of aluminum sand casting is its consistency. With consistent quality and a strong reputation, Cast Rite is dedicated to meeting OEM requirements. For instance, aluminum gear housings are popular among manufacturers.
The primary aluminum sand casting alloy, A360.0, has good corrosion resistance and good machinability. The other two, 380 and 413, are aluminum-tin alloys and are commonly used for engine bearings and pistols. The five-series alloy, on the other hand, has the best corrosion resistance, dilution, and wear resistance. It is expensive, but it has a high degree of machinability, low dilution, and a smooth surface. The grains of aluminum are small and dense, helping the castings to have high mechanical properties.
During the casting process, the molten metal is poured into a mold. During the cooling process, the metal starts solidifying and taking its final shape. The cooling time can be calculated by measuring the thickness of the mold and its temperature. It is during the solidification process that the majority of defects occur. For example, if the parts cool too fast, they might shrink or crack or become incomplete. This can be minimized by taking appropriate precautions when designing the molds and parts.
One of the most important reasons designers choose aluminum over other materials is weight. It is 39% lighter than gray iron. That means a 10lb aluminum shape weighs 26lbs of gray iron. However, this does not mean that weight savings from aluminum will be realized without changes in the manufacturing process. Instead, ribs, thicker sections, or inserts may be added to the casting for added strength. Ultimately, however, the weight savings from aluminum is often less than the benefits of a lighter material.
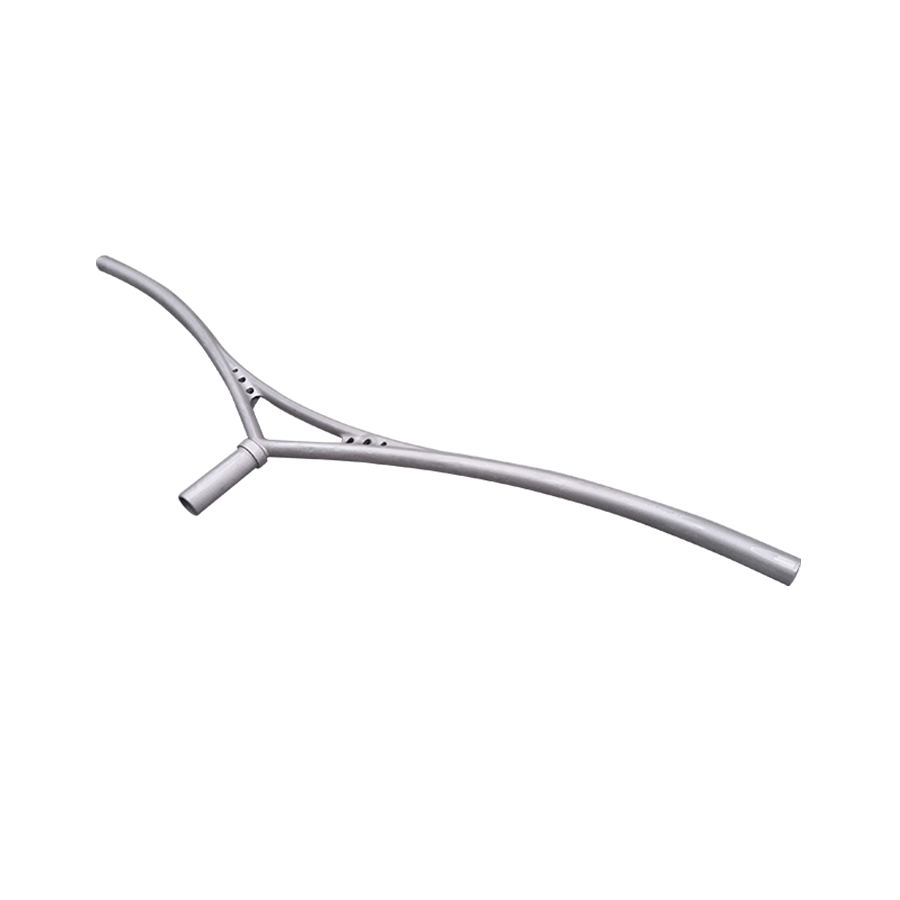
Casting process:Sand-cast
Approximate weight:16kg
Approximate size:2400xφ60
Application:Street light accessories
Product Description
Casting process |
Approximate weight |
Approximate size |
Application |
Sand-cast |
16 |
2400xφ60 |
Street light accessories |