Aluminum Alloy Sand Casting Parts Foundry
The advantages of aluminum alloy sand casting are numerous. It has good yield and tensile properties. The process is easy to automate and recycle. However, this process is limited to small to medium parts. To get the benefits of aluminum alloy sand casting, here are some factors you should consider. Read on to learn more about this process. You will also find out how aluminum alloy sand casting differs from other types of metal casting.
Resign sand casting
A resign sand casting parts foundry uses yellow phenolic resin sand. This is more expensive than furan resin sand, and it is used only one time. It is also used for large iron castings. Both methods use the same gating system. The number of components in a mould box will determine how fast the production rate can be achieved and how much it will cost.
A skilled pattern maker creates a pattern by using a design in a wood, metal or plastic. The sand is then ground, swept or strickled into the desired shape. The pattern must be slightly larger than the finished product. This is called the contraction allowance. For different metals, different rules are used. In the mold, a pattern is placed and a mold is formed.
High tensile properties
There are several types of aluminum alloys used for casting parts. All of them possess a wide range of properties, including high strength and tensile resistance. In addition, they offer good weldability, good machinability, and corrosion resistance. The most common type of aluminum alloy sand casting is LM25, which is a high-strength alloy with excellent tensile properties. Among the other types of aluminum alloys, BSL169 is the primary alloy, extracted from bauxite. Compared to LM6, BSL169 has a higher elongation and is used on many high-spec MOD applications. LM13 alloy is also widely used, and has good tensile and compression properties.
In addition to comparing the strength and tensile properties of the two types of aluminum alloys, the study also evaluated the impact of recycled metal versus virgin metal. The degassing process, which involves bubbles of argon through a degassing unit, was used to control the hydrogen content of the metal. This level of hydrogen was maintained to 0.1 ml/100 g Al during mold pours. Finally, a reduced pressure test was performed to measure the porosity of the melt solidified under reduced pressure. The test was performed at 2.6 specific gravity at 1,300F.
Good yield
High volume sand casting requires a substantial investment in automated equipment and floor space. The yield is often less than 50%, requiring more finishing and machining. Sand castings are prone to slow cooling rates, especially in thick sections, leading to poor mechanical properties and higher porosity. Other considerations include sand consistency, volume, and quality, and disposal. These factors can greatly reduce yield.
While many designers choose aluminum for its lighter weight, the process is not always as straightforward as that. While aluminum is more lightweight than iron, designers must be aware that the weight savings will not be the same as when using gray iron. Because of the lighter material, they may need to add inserts, ribs, or thicker sections to get the same strength and rigidity. Additionally, they may be required to reduce the weight of the cast.
While the sand casting process does not yield as much material as other methods, it is a cost-efficient way to produce large volumes of high-quality aluminum parts. A good yield aluminum alloy sand casting foundry will use a heat-reactive resin system and a mold to create the sand-cast parts. While aluminum alloy sand casting is not as efficient as other casting processes, the process is more flexible, and it is an excellent choice for high production volumes.
Easy to work with
Aluminum Alloy Sand Casting Parts foundry is an excellent choice for a variety of manufacturing applications. This process is easy to work with and can be a cost-effective solution for many different parts. Its ease of use makes it ideal for a variety of industries, including aerospace, medical, and industrial. It is also easy to work with because the molds are made of wood or aluminum.
Once a mold is made, it is placed inside the foundry. The mold is coated with lubricant and placed in a thermoset sand chamber. Once the mold is hardened, the pattern is removed. The two halves of the mold form a complete mold. Once the mold is complete, the liquid aluminum is poured inside. This process solidifies the part, and the finished product is ready for machining.
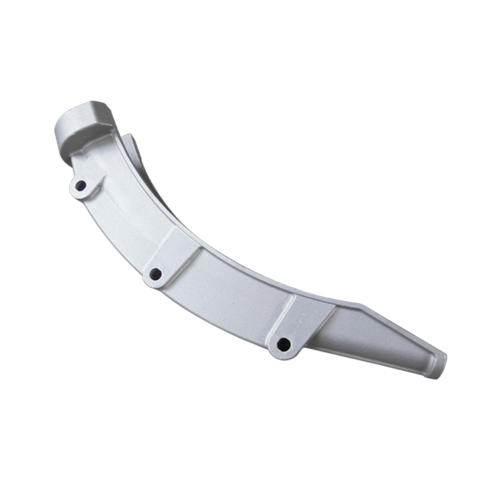